The Achilles’ Heel of Automation: Why Robot Security Can’t Be an Afterthought in Manufacturing
Key Takeaways
Automation is the golden key to industrial progress. But with great power comes great responsibility. And as robots take on ever-more complex tasks, a clear vulnerability emerges: security. From operational disruptions to safety concerns, the fallout from a cyberattack on an industrial robot is far-reaching.
This blog delves into the soft underbelly of automation. We’ll explore why prioritizing robot security is no longer an afterthought but essential for any modern manufacturing operation.
The Rise of the Robots
Robots in manufacturing automation aren’t new. In 1962, Unimation created UNIMATE, the first robot used by a significant manufacturer, General Motors. However, it wasn’t until the 1980s that robotic manufacturing really took off. This year, the total number of operational robots globally hit a new record of about 3.9 million units.
Let’s discover how some robots take the heavy lifting (literally) out of manufacturing:
- Articulated robots: Generally considered the most versatile robots, they have multiple joints mimicking human arms. Therefore, articulated robots are ideal for tasks like welding, painting, and material handling.
- Collaborative robots (cobots): Typically smaller and lighter than most industrial robots, they were designed to work safely alongside humans. For example, cobots can be programmed for assembly tasks, like inserting components or tightening screws.
- SCARA robots: These are well-suited for high-speed precise inspections. With their fast and efficient movements, they can inspect numerous products on a conveyor belt, looking for defects like missing parts.
Robots can operate 24/7, meaning a major benefit in manufacturing is their increased output compared to human labor. Additionally, robots can perform tasks quickly and repeatedly, reducing human fatigue-related errors and boosting production consistency.
These machines can also handle dangerous tasks like heavy lifting or working with hazardous materials, decreasing the risk of worker injuries. One study proves this. It shows that an increase in robot presence by one standard deviation (1.34 robots per 1,000 workers) is associated with a decrease of approximately 1.2 injuries per 100 full-time workers.
Why Robot Security Matters
While the benefits of automating manufacturing with robotics are clear, a new issue is emerging. Industrial robots are increasingly connected to factory networks, allowing remote monitoring, data transfer, and programming updates. While beneficial, network connections act as entry points for hackers to access the network and infiltrate the robot’s control system.
There’s a full spectrum of issues that unsecured robots can cause, including:
- Data breaches: Robots often collect and store sensitive data, such as production schedules, product designs, or intellectual property. If a robot’s system is compromised, this data could be stolen or leaked, causing financial and reputational damage.
- Robot control: Hackers could gain access to robot control systems and manipulate their movements. This could lead to production disruptions, damage to equipment or even physical harm to workers.
- Supply chain disruption: Robots are increasingly integrated into complex manufacturing networks. A successful cyberattack on a single robot could disrupt the entire supply chain, leading to production delays and financial losses.
One example of malware affecting industrial machinery was Stuxnet, a computer worm designed in 2010 to disable a key part of the Iranian nuclear program — and the first known cyber weapon. Stuxnet targeted industrial control systems like those managing uranium centrifuges. It infiltrated computers, identified PLCs (industrial machinery controllers) and manipulated their programming to spin centrifuges erratically, causing damage or destruction. The virus ultimately delayed Iran’s nuclear program by at least two years.
Beyond the Firewall: Traditional IT vs. Robot Security
Traditional IT security is a strong base for robot security, but their differences require more specialized measures.
For example, unlike typical computers, robots are physically connected to their environment. So, while a compromised computer might leak data, a hacked robot could cause physical damage, injuring workers and disrupting production by malfunctioning. Furthermore, unlike servers — under lock and key — robots operate on factory floors, making them vulnerable to tampering.
What’s more, modern robots are complex, combining various software like operating systems (OS) and control programs. So, as robots become integrated with factory networks, this creates a larger attack surface, which is exacerbated by older robots, often using outdated OS with known weaknesses.
Manufacturers need comprehensive security, encompassing both IT and robot defenses. Imagine a fortified castle: strong IT security acts as the moat, while robot-specific security functions as drawbridges. Only through robust digital and physical safeguards can manufacturers ensure a safe and reliable robotic workforce.
Proactive Risk Management Strategies
So, how can manufacturers leverage a comprehensive security plan for their robotics? Robotic business insurance provides a critical safety net to prevent both business setbacks and even closures. But manufacturers can also start with a roadmap to fortify their robot security posture.
- Vulnerability assessment: Before fortification, manufacturers must conduct regular security audits of robots and factory networks to identify software, hardware and network configuration vulnerabilities. Third-party security specialists can be valuable partners in this process.
- Access control and user authentication: Implement the principle of least privilege for robot access which grants users only the minimum permissions necessary to perform their tasks. Plus, using multi-factor authentication for access to robot systems and control interfaces adds an extra layer of security beyond passwords.
- Software updates: Automatically update robot software and firmware whenever security patches become available. Ensure the IT team prioritizes critical patches and tests them thoroughly before deployment. Remember to develop a secure decommissioning plan for robots using outdated OS.
- Network segmentation: If feasible, segment robot networks from traditional IT infrastructure. This can limit the damage from a compromised robot by preventing it from accessing critical IT systems easily.
- Employee training: Provide regular cybersecurity training for all employees interacting with robots, including programmers, maintenance personnel, and operators. Teach them how to identify suspicious activity, report security incidents and follow security best practices.
Collaboration is Key: Building a Security Ecosystem
For manufacturing automation to continue going from strength to strength, manufacturers, robot vendors and cybersecurity experts must bring their unique expertise.
For example, manufacturers understand their specific needs and deployment environments, whereas robot vendors have in-depth knowledge of their robots’ hardware and software. On the other hand, cybersecurity experts offer specialized skills in threat detection and vulnerability analysis. Together, they can develop comprehensive security solutions, share knowledge, and standardize security protocols.
Also, sharing information about new vulnerabilities and attack techniques allows everyone to be on the lookout for suspicious activity. Manufacturers can be alerted to potential exploits targeting the specific robots they use, and vendors can prioritize patching newly discovered vulnerabilities in their software. By sharing data on past attacks and attempted breaches, security experts can identify patterns and emerging trends.
The Future of Robot Security: Emerging Trends
The future of robot security is brimming with innovation. Here’s a glimpse into some exciting trends that hold promise for a more secure future:
- AI-powered threat detection: Robots generate vast quantities of data through sensors and operational logs. Machine learning and AI algorithms can analyze this data to identify anomalies indicating suspicious activity or potential security breaches. This allows for proactive threat detection and possible intervention before an attack occurs.
- Blockchain for secure data storage: Blockchain technology can create an immutable record of robot activity and data logs. This tamper-proof record can be used to identify unauthorized access or data manipulation attempts. Furthermore, blockchain can secure communication between robots and other systems, preventing unauthorized data interception.
- Standardization: Currently, robot security varies greatly depending on the manufacturer and OS. Standardized security protocols would establish minimum security requirements for all robots, making them more secure by default.
There’s no need for robot security to be the chink in the armor of manufacturing automation. By prioritizing robot security measures from the outset, manufacturers can harness the full potential of automation while mitigating the associated risks.
Insurance Rebuilt, End-to-End
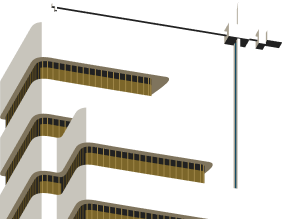